SmCo magnets (also called Samarium Cobalt magnets) are consist of Sm (samarium), Co (cobalt) and other elements like Hf(hafnium) or Zr(zirconium), they are part of permanent rare earth magnet family, there are two main types, the composition of SmCo5 is: samarium 37% and cobalt 63%, while Sm2Co17 is: samarium 25%, copper 5%, iron 18%, hafnium or zirconium 2%.
The advantages of SmCo magnets are: strong magnetic strength, high temperature resistance, and reliable performance against corrosion, they can keep their magnetic properties in very high temperature conditions, the maximum working temperature of SmCo5 is 250℃, while Sm2Co17 is 350℃.
Types of SmCo Magnets

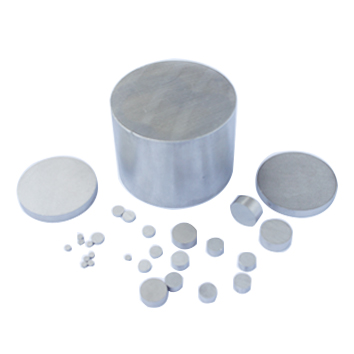

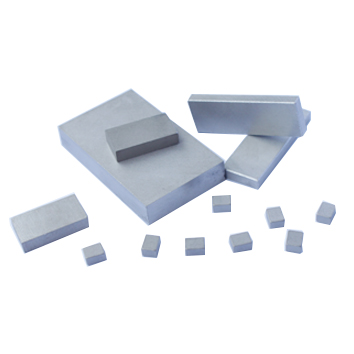

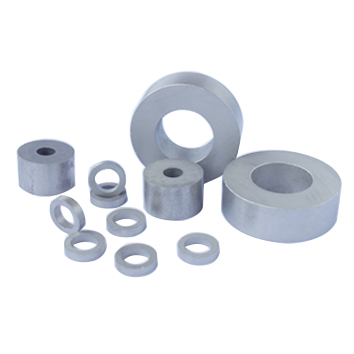

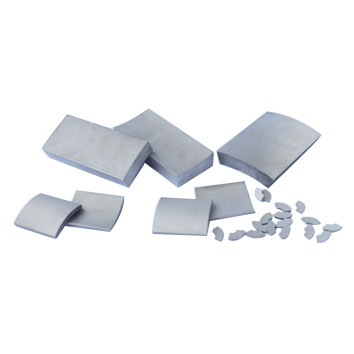

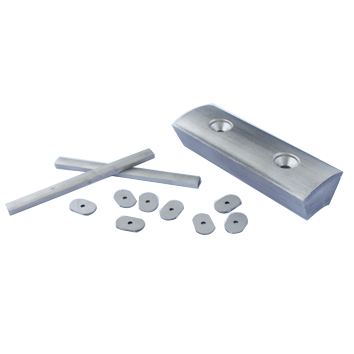
Magnetic properties
Manufacturing method
SmCo magnets are produced by sintering process, but also can be produced by injection molding and compression bonding, for sintered SmCo magnets, samarium, cobalt and other transition metals will be made into micro size SmCo powders, these powders are compacted into a rigid steel mould and pressed, after that sintered at a very high temperature, similar shapes as final product will be produced, then machined to final size with a good surface finish.
SmCo magnets are hard and brittle, they are easily chipping and cracking, so the machining must be done by the water-cooled diamond-coated grinding machine.
Magnetizing & Surface treatment
All SmCo magnets are anisotropic, they are treated and cooled in a magnetic field, then oriented with a preferred magnetic direction with maximum magnetic direction, extreme high magnetic field is required due to high coercive force, they can only be magnetized along the oriented direction, multi-poles magnetized is also possible with special magnetizing fixture.
The corrosion resistant of SmCo magnets are considered good, no surface coating is necessary, but the coatings like NiCuNi, Zn, Black epoxy can be plated if required.
Applications
SmCo magnets are widely used in the wind, power, medical, aerospace, military, automotive, semiconductor, oil and energy industry of very high or low temperature environments, the most common applications are: wind turbine equipment, electric motors, turbo machinery, medical devices, accelerometer, particle accelerators, magnetic couplings, sensor systems, magnetic separation devices, high performance motors, actuators, automation equipments, robotic arms, pipeline inspection, magnetic bearings, traveling wave tubes, robotic arms, magnetic drive components, generators, energy recovery systems, pipeline inspection, magnetic bearings and more.