We are your good partner for anything magnetic. Since established, we are improving our product range continuously, our main products are all kinds of rare earth permanent magnets, flexible magnets, holding magnets and magnetic tools. What we supplied is not only high quality products, but also very professional service.
We are always ready to assist you to work out suitable solutions at reasonable and competitive prices. With great efforts we have been doing everyday, we become a professional and superior magnet manufacturer and serving different fields of different applications, both industrial and daily use.
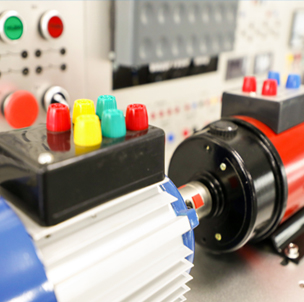
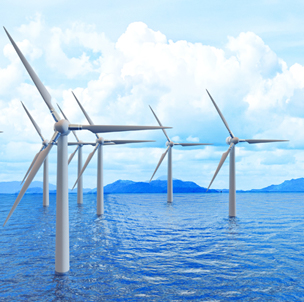
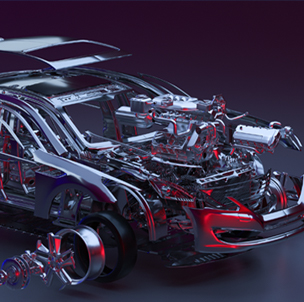
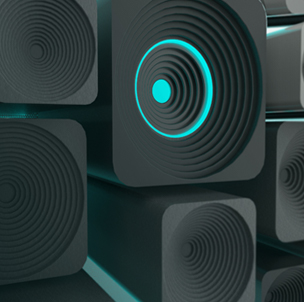
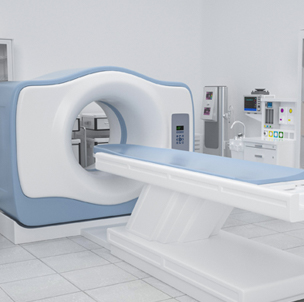
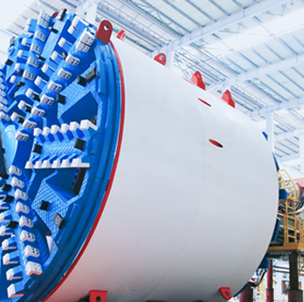
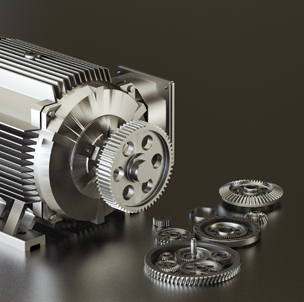
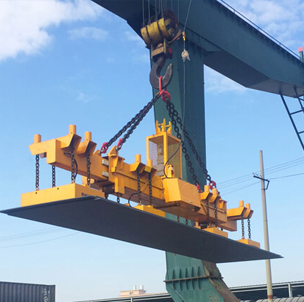
Permanent magnets are the majority of magnetic materials nowadays, they are made of ferromagnetic alloys like rare earth metals and minerals. The main types available in our factory are: Neodymium magnets, SmCo magnets and AlNiCo magnets. After the materials are magnetized, they can create a consistent and indefinite magnetic strength without any external of magnetic field or electrical power.

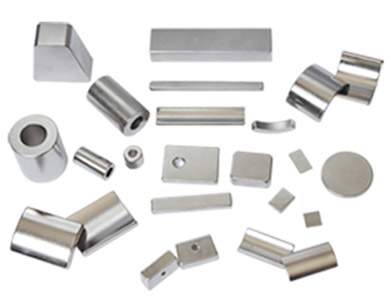
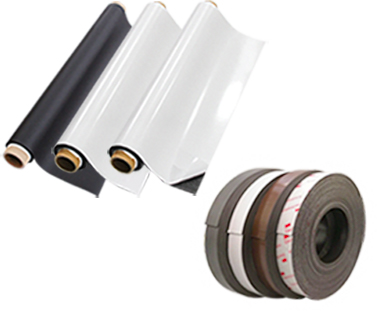
Flexible magnets (also called rubber magnets, soft magnets) are made of strontium ferrite powder compounded with plastics or rubbers (NBB or CPE). The main 3 grades of flexible magnets are Isotropic, Semi-anisotropic, Anisotropic, with magnetic properties with (BH)max from 0.6 MGOe to 1.6 MGOe. Flexible magnets are flexible and soft, so can easily be cut to the shape size required by using a knife, also easily bent, twisted, slit, or coiled, no magnetic properties will lose during this.

Holding magnets are also known as pot magnets or mounting magnets, which can be assembled with hook, eyebolt or any other accessories. With a strong magnet encased in a steel cup, all the magnetic fields are centralized on one side, this makes the magnetic force much bigger than magnet alone. The inside magnet can be neodymium, smco, alnico or ferrite, you can choose the most suitable material by its application, while the steel cup protects the magnets against chipping and cracking.

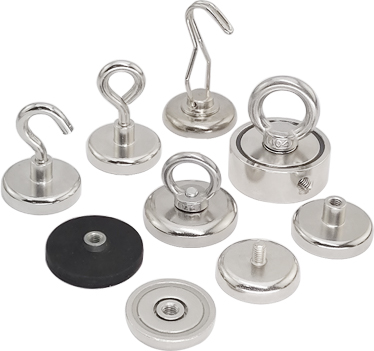
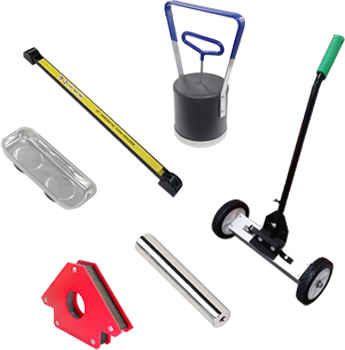
Magnetic tools are versatile tools consist of magnets with other materials, different magnetic tools are widely used in both industrial and daily life. We can produce a wide range of magnetic tools, including tube and grid magnets, welding magnets, magnetic pickup tools, magnetic sweepers, magnetic tool holders, badge magnets, magnetic clips, button magnets etc. We can also produce custom magnetic tools and are happy to assist you to make your design, our magnet engineers have many years experiences in the magnetic field, an efficient and useful tool can be definitely worked out for your application.

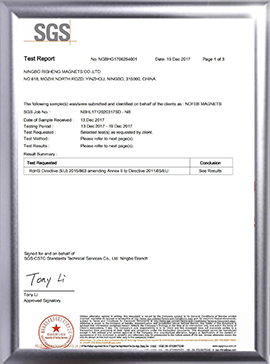
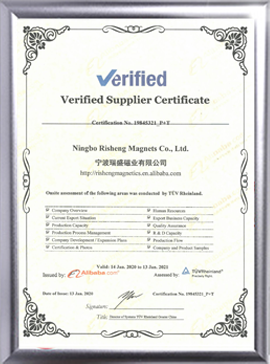
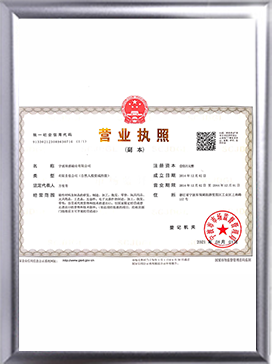
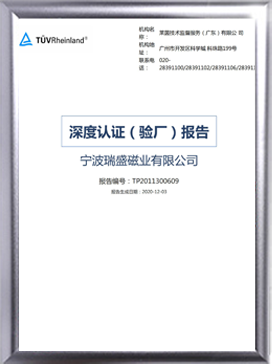
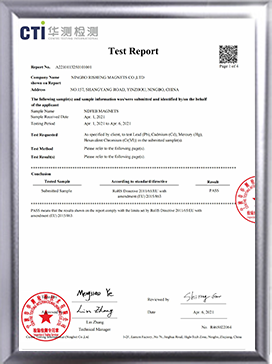
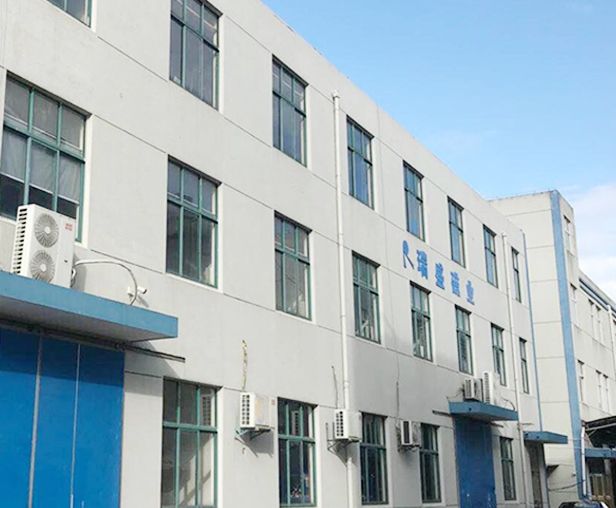
We are one of the world's leading companies in the field of magnet
technology. Since its establishment, we have been focusing on designing
and manufacturing high-tech permanent magnets, magnet components
and industrial magnet systems. We can not only provide you with
standard magnets but also produce customized magnets and magnetic
components to meet different specific needs.
We offer a wide range of work holding systems, magnet assemblies,
workshop tools, lifting and handling systems, industrial filters, etc. for
the global market. Our advanced high-tech production equipment can
guarantee to provide customers with stable high quality and customization.
We are striving to continue to develop in order to maintain the market's technological leadership by providing customers with innovative and tailor- made magnetic solutions.
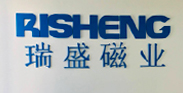
We are a professional magnet factory and have been focusing on the magnetic field since founded, we are providing high quality magnets for different applications today, for both esteemed industrial and commercial companies.
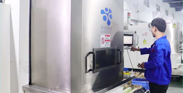
We have a complete of production lines of different magnets and magnetic assemblies, making a wide product range including Neodymium magnets, Flexible magnets, Holding magnets and Magnetic tools.
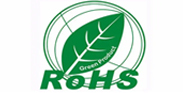
We are certificated by TUV Rheinland Magnagement Sytem, all our magnets will be produced with every production process done under extremely strict quality control standard, also all our magnets meet RoHS standards certificated by SGS China.

We are fully equipped to manufacture custom magnets, our advanced machines has capabilities to produce complicate shapes, we welcome our customers to do their design, the requested requirments will be met.
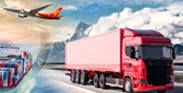
We can produce the magnets very quickly by our advanced equipments, our production volume is over 1,000 tons every year and we carry a huge stock of standard magnets in our stock for fast delivery.
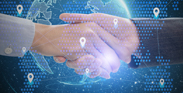
The most important thing for us is to make sure every customer feel satisfied working with us, we are serving over 100,000 customers and will provide a professional and friendly customer service from the beginning to the end.